Assembly Automation Case Studies: Pallet assembly system for metal pressed parts
Explore the Assembly Automation Section
Automatic assembly machines and automation system solutions provide the best method for reducing labour costs, increasing output and eliminating manual handling concerns.
Explore this section to find out more about the how TQC can help you with your factory assembly automation processes
- Assembly Automation
- Pallet Transfer Systems
- Rotary Systems
- Assembly Benches
- Robotics and Handling
- Checking Jigs & Assembly Fixtures
- Case Studies
- Casting Multi-Position Screwdriving & Marking System
- Co-operating Robots
- Pallet Assembly System for Automotive Glovebox Latch
- Pallet Assembly System for Metal Pressed Parts
- Laser Marking & Verification System
- Lead Pot Robotic Handling System
- Automotive Plug Feed & Check System
- Poka Yoke Assembly Bench for Automotive Latch
- Bearing Automatic Heat, Press & Assembly System
- Hot Insert, Cold Insert & Seal Assembly/Check System
- Robotic Handling & Leak Test Cell
- Robotic Weld & Fabrication System
- SCARA Robot cell for Automatic Assembly of a Small Electrical Handset
- Semi-Automatic Assembly System for Automotive Radiators
- Cylinder Head Cover Clean, Assemble and Test Suite
- Automotive Hinge Assembly & Test System
Client: Automotive Parts Manufacturer
Part: Seat Recliner Mechanism
Machine supplied: Two Pallet assembly systems, Dedicated Assembly Machine and Rotary Assembly Machine
Overview: This suite of equipment was designed and manufactured in order to give the customer the ability to assemble and test a new automotive assembly within their production environment. TQC developed this system alongside the client to allow them to produce high speed and quality controlled parts for their automotive customer.
Download details of this system as a PDF
Key features:
- Four machine assembly suite for the automotive industry
- Pallet transfer systems, dedicated assembly machine, rotary indexing system
- Fully automatic and semi-automatic operation
- Integrated technology modules such as press unit, grease application and parts feeding
This engineering project covered the supply of a suite of special assembly machines for an industrial automation cell. The automated production line consisted of four machines to automatically assemble and function test an automotive seat recliner mechanism. One machine was a fully automatic machine using vibratory bowl feeding of parts plus pick and place mechanisms to assemble 2 metal parts together. The 2 parts are pneumatically pressed together with a load monitoring facility.
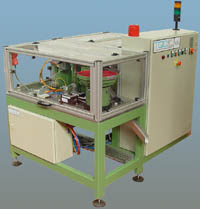
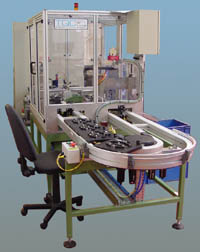
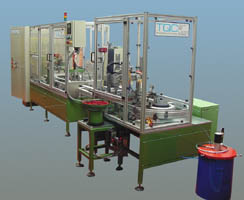
Three machines supplied as part of a four machine suite of automation equipment
A further machine was based on a rotary indexing carousel turntable. The machine was semi-automatic in operation with an operator loading the metal pressings to be assembled into a fixture nest and then unloading the completed assembly. A parts verification or poke yoke test was carried out on one station and an automatic spin riveting operation on another station. Automatic load and position monitoring was used during the spin riveting operation. The completed sub assembly was function tested.
The remaing two machines were both pallet based assembly machines using a twin track flexlink conveyor system. One machine was semi automatic in operation with manual work stations and automatic stations combined. The machine had automatic press rivet and plunge rivet operations. The production machine also included an automated greasing station.
The other pallet transfer system included automated rivet assembly stations, function testing with automatic setting of the part to the correct position for delivery, plus an automatic print and apply labelling station.
Rotary indexing system with spin riveting operation
To find out more about how we can help you with your pallet transfer and assembly systems:
We build all machines in-house, applying our 25+ years experience in specialised test and automated handling machines to the engineering projects we undertake. We offer customer support, backup and service call-out for all projects, whatever the size.
Get in touch with us to discuss your requirements and we will be happy to offer our professional advice and visit you at your site.
- Contact us online
- Email us or call us on 0115 950 3561