Assembly Automation Case Studies: Cleaning, assembling and testing Nissan cylinder head covers
Explore the Assembly Automation Section
Automatic assembly machines and automation system solutions provide the best method for reducing labour costs, increasing output and eliminating manual handling concerns.
Explore this section to find out more about the how TQC can help you with your factory assembly automation processes
- Assembly Automation
- Pallet Transfer Systems
- Rotary Systems
- Assembly Benches
- Robotics and Handling
- Checking Jigs & Assembly Fixtures
- Case Studies
- Casting Multi-Position Screwdriving & Marking System
- Co-operating Robots
- Pallet Assembly System for Automotive Glovebox Latch
- Pallet Assembly System for Metal Pressed Parts
- Laser Marking & Verification System
- Lead Pot Robotic Handling System
- Automotive Plug Feed & Check System
- Poka Yoke Assembly Bench for Automotive Latch
- Bearing Automatic Heat, Press & Assembly System
- Hot Insert, Cold Insert & Seal Assembly/Check System
- Robotic Handling & Leak Test Cell
- Robotic Weld & Fabrication System
- SCARA Robot cell for Automatic Assembly of a Small Electrical Handset
- Semi-Automatic Assembly System for Automotive Radiators
- Cylinder Head Cover Clean, Assemble and Test Suite
- Automotive Hinge Assembly & Test System
Client: Global Automotive Plastics Company, end user Nissan
Part: Plastic Cylinder Head Cover
Machine supplied: Three machine suite assembly for Nissan cylinder head cover
Overview: This system was designed and manufactured in order to give the customer the ability to assemble and test a cylinder head cover for Nissan within their production environment. TQC developed this system alongside the client to allow them to supply quality assured products to Nissan.
Download details of this system as a PDF (page 1), Download details of this system as a PDF (page 2)
Key features:
- Three machine suit of automation equipment
- Leak Test Machine
- Oil Seal Insertion Machine
- Weld Debris Removal Machine
- Manual loading and unloading
- Automated assembly and testing functions
- Technology modules incorporated including leak test instruments and connectors

Leak test machine
Leak test machine
This machine was designed to check for the presence of 4 brass inserts and to perform 4 bi-directional leak tests on the 4 oil seals.
Key features:
- Light guard access for manual load/unload
- Furness Controls Leak Test Units
- Twin pillar leak test fixture
- Eight leak tests performed
- Presence check for 4 Brass Inserts
- Pryor percussion marker
- Mitsubishi FX PLC Control
- GT1155 colour touch screen graphical HMI
- Maximum leak rate of 1cc/min @ 0.2 bar
- 50 second cycle time
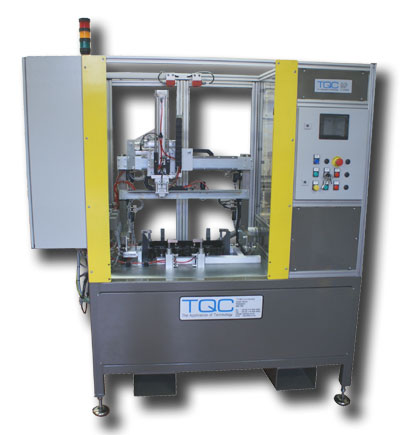
Oil seal insertion machine
Oil seal insertion machine
This machine was designed to automatically insert 4 oil seals into the CHC Moulding and check for Presence, correct insertion depth and orientation.
Key features:
- Light guard access for manual load/unload
- 4-position, 2-axis gantry
- Seal orientation & position detection
- Pass mark Mitsubishi FX PLC
- GT1155 colour touch screen graphical HMI
- Removable tooling
- 40 second cycle time

Weld debris removal machine
Weld debris removal machine
This machine was designed to check for blockage in two internal ports on the baffle plate and vacuum clean weld debris from inside the baffle plate cavity.
Key features:
- Light guard access for manual load/unload
- Port blockage test
- Debris cleaning via vacuum connection and part vibration connected to an industrial vacuum cleaner
- Automatic connection and sealing to 4 openings
- Pass mark
- Mitsubishi FX PLC
- 50 second cycle time
To find out more about how we can help you with your automated or semi-automated assembly systems:
We build all machines in-house, applying our 25+ years experience in specialised test and automated handling machines to the engineering projects we undertake. We offer customer support, backup and service call-out for all projects, whatever the size.
Get in touch with us to discuss your requirements and we will be happy to offer our professional advice and visit you at your site.
- Contact us online
- Email us or call us on 0115 950 3561