Assembly Automation Case Studies: Hot and cold insert and seal assembly and checking system
Explore the Assembly Automation Section
Automatic assembly machines and automation system solutions provide the best method for reducing labour costs, increasing output and eliminating manual handling concerns.
Explore this section to find out more about the how TQC can help you with your factory assembly automation processes
- Assembly Automation
- Pallet Transfer Systems
- Rotary Systems
- Assembly Benches
- Robotics and Handling
- Checking Jigs & Assembly Fixtures
- Case Studies
- Casting Multi-Position Screwdriving & Marking System
- Co-operating Robots
- Pallet Assembly System for Automotive Glovebox Latch
- Pallet Assembly System for Metal Pressed Parts
- Laser Marking & Verification System
- Lead Pot Robotic Handling System
- Automotive Plug Feed & Check System
- Poka Yoke Assembly Bench for Automotive Latch
- Bearing Automatic Heat, Press & Assembly System
- Hot Insert, Cold Insert & Seal Assembly/Check System
- Robotic Handling & Leak Test Cell
- Robotic Weld & Fabrication System
- SCARA Robot cell for Automatic Assembly of a Small Electrical Handset
- Semi-Automatic Assembly System for Automotive Radiators
- Cylinder Head Cover Clean, Assemble and Test Suite
- Automotive Hinge Assembly & Test System
Client: Global Automotive Plastics Company
Part: Plastic Throttle Body
Machine supplied: Hot Insert, Cold Insert and Seal Assembly/Checking System
Overview: This system was designed and manufactured in order to give the customer the ability to process throtte body mouldings within their production environment. TQC developed this system alongside the client to allow them to automatically insert parts, check the presence of seals and ensure quality controlled parts were delivered to their customer.
Download details of this system as a PDF
Key features:
- Twin track vibratory bowl feeder
- 3 Axis servo controlled manipulator for hot insertion
- 2 Position fixture transfer shuttle
- Poka Yoke sensing of moulding features, compression limiters and threaded inserts
- Temperature controlled stainless steel heater blocks
- Mitsubishi FX PLC control and colour touch screen graphical HMI
- Light guard
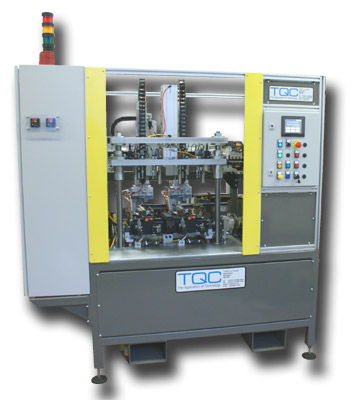
Hot insert, cold insert seal assembly system built by TQC for plastics
moudlings client in the automotive industry
This machine was produced for an automotive plastics moulding manufacturer to automatically insert 6 threaded brass inserts and 3 steel compression limiters into a Throttle Body Moulding. The threaded inserts are pressed into the moulding after heating them to a temperature of approximately 350 deg C and are then air cooled. The inserts are checked for correct insertion depth, with a tolerance of flush to 0.2mm proud maximum.
The compression limiters are pressed into the moulding at an ambient temperature to achieve a cycle time of 1 moulding every 20 seconds, the machine processes a pair of moulding every 40 seconds.
The mouldings are manually loaded in pairs onto the locating fixtures at the front of the machine along with 6 compression limiters. If all parts are present and correct the cold insertion is automatically performed at the front station and if successful the fixture transfers the parts to the rear station for hot insertion.
Good assemblies are returned to the front station for the manual fitting of a seal with positional verification and a single character pass stamp.
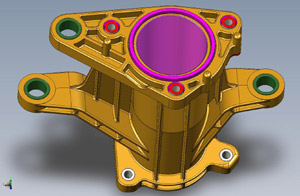
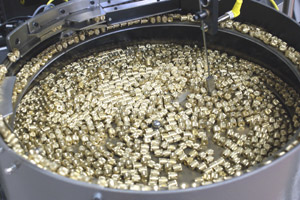
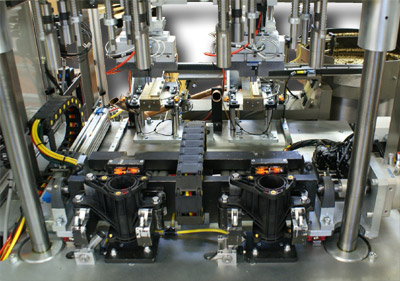
Details of the hot insert, cold insert seal assembly system
To find out more about how we can help you with your automated assembly or hot and cold insert systems:
We build all machines in-house, applying our 25+ years experience in specialised test and automated handling machines to the engineering projects we undertake. We offer customer support, backup and service call-out for all projects, whatever the size.
Get in touch with us to discuss your requirements and we will be happy to offer our professional advice and visit you at your site.
- Contact us online
- Email us or call us on 0115 950 3561