Assembly Automation Case Studies: Automatic bearing induction heating and pressing assembly system
Explore the Assembly Automation Section
Automatic assembly machines and automation system solutions provide the best method for reducing labour costs, increasing output and eliminating manual handling concerns.
Explore this section to find out more about the how TQC can help you with your factory assembly automation processes
- Assembly Automation
- Pallet Transfer Systems
- Rotary Systems
- Assembly Benches
- Robotics and Handling
- Checking Jigs & Assembly Fixtures
- Case Studies
- Casting Multi-Position Screwdriving & Marking System
- Co-operating Robots
- Pallet Assembly System for Automotive Glovebox Latch
- Pallet Assembly System for Metal Pressed Parts
- Laser Marking & Verification System
- Lead Pot Robotic Handling System
- Automotive Plug Feed & Check System
- Poka Yoke Assembly Bench for Automotive Latch
- Bearing Automatic Heat, Press & Assembly System
- Hot Insert, Cold Insert & Seal Assembly/Check System
- Robotic Handling & Leak Test Cell
- Robotic Weld & Fabrication System
- SCARA Robot cell for Automatic Assembly of a Small Electrical Handset
- Semi-Automatic Assembly System for Automotive Radiators
- Cylinder Head Cover Clean, Assemble and Test Suite
- Automotive Hinge Assembly & Test System
Client: General Engineering Company
Part: Bearing Assembly
Machine supplied: Bearing Heating and Pressing Assembly System
Overview: This system was designed and manufactured in order to give the customer the ability to produce the required assemblies within their production environment. TQC developed this system alongside the client to allow them to automatically feed, press and assembly parts, checking was included to ensure correct parts were supplied to their customer.
Download details of this system as a PDF
Key features:
- Vibratory bowl feeders
- Two position twin head part transfer system for main body
- Dedicated pick and place system to load parts into press top tool
- 10kW Induction heating coil
- Hydraulic press with heated bottom tool
- Non contact temperature monitoring
- Load / position monitoring
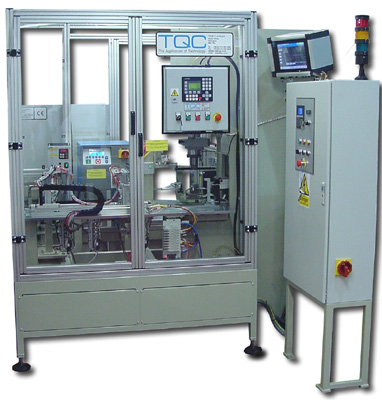
Bearing heating and pressing assembly system installation
This fully automatic system receives bulk product and assembles the 2 parts of a bearing assembly by heating the main body and then pressing the second part into a feature on the body. The whole process runs on a 10 seconds cycle time.
Vibratory bowl feeders orientate and singulate parts, the bodies are transferred into an induction coil, once heated placed they are placed into heated bottom tooling of a hydraulic press.
The upper part is fed by the second bowl with individual parts loaded into the top tool of the press. Temperature, load and position monitoring are used to ensure correct press assembly. Assembled parts are located by the press top tool and released onto a advancing outfeed conveyor system.
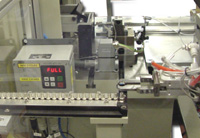
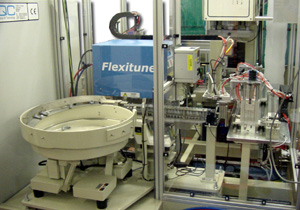
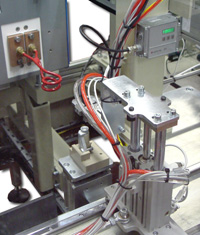
Details of the bearing heating and pressing system built by TQC
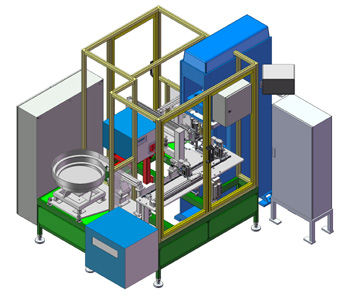
Design overview of the complete assembly system
The system accommodates a single size of stud at any one time, but is adjustable for sizes from M10 to M20, the overall throughput was 20 studs per minute.
To find out more about how we can help you with your automated assembly, robotic or special handling systems:
We build all machines in-house, applying our 25+ years experience in specialised test and automated handling machines to the engineering projects we undertake. We offer customer support, backup and service call-out for all projects, whatever the size.
Get in touch with us to discuss your requirements and we will be happy to offer our professional advice and visit you at your site.
- Contact us online
- Email us or call us on 0115 950 3561