Leak Testing: Air Decay - High Pressure (Over 6 bar)
Explore the Leak Testing Section
Leak Testing is used to ensure quality, tested and proven parts are supplied into the market. The use of leak testing equipment eliminates failures in the field.
Explore this section to find out more about the how TQC can help you with your leak testing requirements
- Overview
- Air Decay
- Helium
- Other Test Methods
- Leak Testing Services
- Standard Equipment
- Case Studies
- Automotive Brake Leak and Flow Testing
- Automotive Bedplate Leak Test Machine
- Battery Tray Leak Test Machine
- Chilled Beam Leak Test
- Flexible Leak Test Facility
- Fuel Tank Leak Testing
- Helium Leak Test Bench
- Helium Leak Testing of Automotive Fuel Pipes
- High Pressure Audit Leak Testing System with Datalogging
- High Speed Leak Testing of Pipe Fittings using Air and Helium
- High Speed Leak Testing of Plastic Vial for the Medical Industry
- Leak Test Facility for Water Valves
- Leak Test Cell with Robotic Handling
- Casting Leak Testing of Engine Blocks
- Medical Filter Leak Test Machine
- Medical Showerhead Leak Test Machine
- Plastic Fuel Rail Leak and Burst Test Machine
- Plastic Sump Pipe Leak Test and Assembly
- Small Medical Device Leak Test Machine
- Twin Station Leak Test Machine for Oils Sumps
- V6 Cylinder Head Leak Test Machine
- V6 Engine Leak Test Machine
- V8 Cylinder Head Leak Test Machine
- V8 Engine Block Leak Test Machine
- Valve Block Leak Test Machine
- Vauxhall Leak Test Machine
- Weapon Leak Test Machine
TQC provide air decay leak testing solutions for all types of components to measure air pressure decay.
For these solutions, standard leak testing measurement instruments are incorporated to find drop off in air pressure or air flow on the components being tested.
TQC offer test pressures between vacuum and, typically, 16bar (150psig) as standard, with leaktesting measurements down to a resolution of 1 atm.mm3/sec. All air decay leak test parameters may be programmed into the instruments supplied as part of the solution, and the resulting data is available for subsequent Statistical Process Control (SPC) analysis.
One also has to take further precautions as a catastopic failure of the part under test using high pressure may damage the sensitive measuring instrument. All parts should be proof tested before being leak tested, the pressure should be increased in increments and further equipment such as pressure relief valves, air fuses and burst discs may need to be used.
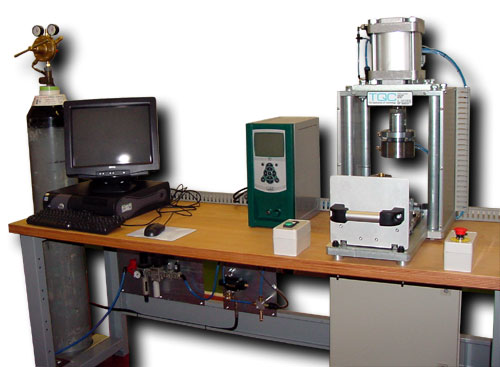
Air decay leak testing facility for sprinklers
High pressure air decay testing (over 6 bar)
The differential testing of parts with higher pressures poses additional challenges for leak testing.
Generally, the high pressure is not suitable for making accurate leak test calculations as it is too unstable.
In these cases one arranges for the test volume to be on the opposite side of the leak path and the instrumentation is arranged to use the differential pressure rise. Parts are placed into a chamber possibly with infill pieces to reduce the test volume as much as possible. With this setup, the internal volume of the test piece can be pressurised to high pressure whilst the test system monitors the pressure in a volume outside the part.
High pressure air decay leak testing is suitable for the following component and environment applications:
- Sprinkler valves
- Hydraulic cylinders
- HIgh pressure regulators
- Munitions
Read more about our Low pressure (0-6 bar) and vacuum leak testing machines.
To find out more about how we can help you with your air decay leak testing requirements:
We build all machines in-house, applying our 25+ years experience in specialised test and automated handling machines to the engineering projects we undertake. We offer customer support, backup and service call-out for all projects, whatever the size.
Get in touch with us to discuss your requirements and we will be happy to offer our professional advice and visit you at your site.
- Contact us online
- Email us or call us on 0115 950 3561