Leak Testing Case Studies: High Speed Leak Testing of Pipe Fittings using Air and Helium
Explore the Leak Testing Section
Leak Testing is used to ensure quality, tested and proven parts are supplied into the market. The use of leak testing equipment eliminates failures in the field.
Explore this section to find out more about the how TQC can help you with your leak testing requirements
- Overview
- Air Decay
- Helium
- Other Test Methods
- Leak Testing Services
- Standard Equipment
- Case Studies
- Automotive Brake Leak and Flow Testing
- Automotive Bedplate Leak Test Machine
- Battery Tray Leak Test Machine
- Chilled Beam Leak Test
- Flexible Leak Test Facility
- Fuel Tank Leak Testing
- Helium Leak Test Bench
- Helium Leak Testing of Automotive Fuel Pipes
- High Pressure Audit Leak Testing System with Datalogging
- High Speed Leak Testing of Pipe Fittings using Air and Helium
- High Speed Leak Testing of Plastic Vial for the Medical Industry
- Leak Test Facility for Water Valves
- Leak Test Cell with Robotic Handling
- Casting Leak Testing of Engine Blocks
- Medical Filter Leak Test Machine
- Medical Showerhead Leak Test Machine
- Plastic Fuel Rail Leak and Burst Test Machine
- Plastic Sump Pipe Leak Test and Assembly
- Small Medical Device Leak Test Machine
- Twin Station Leak Test Machine for Oils Sumps
- V6 Cylinder Head Leak Test Machine
- V6 Engine Leak Test Machine
- V8 Cylinder Head Leak Test Machine
- V8 Engine Block Leak Test Machine
- Valve Block Leak Test Machine
- Vauxhall Leak Test Machine
- Weapon Leak Test Machine
Client: Major International Manufacturer of pipe fittings
Parts: Various water and gas pipe fittings
Machines supplied: Conveyor supplied (fed) fully automatic high speed air decay and helium leak test systems
Overview: This system was designed and manufactured in order to give the customer the ability to test a range of pipe fittings within their production environment. TQC developed this system alongside the client to allow them to 100% test the majority of their range of tees, elbows and reducing fittings from 12mm to 50mm.
Download details of this system as a PDF
Overview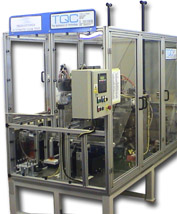
TQC have supplied a suite of 3 automatic leak testing machines that are conveyor fed. The first two machines were designed to 100% leak test numerous variants of welded metal T-pieces, elbows, reducers and adapters used in the water, gas and construction industries. The leak test specification meant that the parts needed to be water tight. The customer then asked TQC to develop a machine to meet the more stringent requirements of testing parts to ensure they are gas tight, and still meet the high production throughputs. TQC met these objectives by integrating helium leak testing technology into the same handling concept of the first two machines.
- Rotary indexing machine
- Automated load / unload
- Twin chamber with interchangable tooling for multiple variants
- Combination leak test using high pressure internally & high pressure vacuum externally
- High speed leak test
- Water and gas tight leak specification met using air or helium as test medium
- Testing to leak test threshold of 1mm3/sec (1x10-6 mbar.l.sec-1)
Handling System
A twin gripper pick and place system was used to load parts from a conveyor pallet to the test fixture and then remove the parts after testing. Twin chamber test fixtures mounted on a rotating table were used to allow automated load and unload whilst meeting the high throughput.
Air Test Medium
Two of the latest generation Nolek S9 leak test instruments tested each component. Both internal high pressure and external vacuum was used to stress the part under test correctly and to provide a short cycle time leak test
Helium Test Medium
The test process required the part to be evacuated, low pressure helium inserted for a gross leak test, then high pressure helium for a fine leak. On completion, the helium was removed from the part and the part stabilised with air.
The system included monitoring of any leaking helium this allows fast testing and minimises helium loss by part leakage.
Varian mass spectrometers have been integrated to monitor the helium gas, with a trigger point used to indicate a leaking part. The leak test threshold that was set by the customer was 1mm3/sec (1 x 10-6 mbar.l.sec-1).
A helium reuse system was integrated into the test machine, this automatically monitored the gas quality and purged the system once the helium was below a set concentration. By including the recovery system typically 50 -100 parts (depending on internal volume) can be tested before the helium needs to be replaced.
To find out more about how we can help you with your high speed or complex leak testing requirements:
We build all machines in-house, applying our 25+ years experience in specialised test and automated handling machines experience to the engineering projects we undertake. We offer customer support, backup and service call-out for all projects, whatever the size.
Get in touch with us to discuss your requirements and we will be happy to offer our professional advice and visit you at your site.
- Contact us online
- Email us or call us on 0115 950 3561