Leak Testing: Water submersal dunk tank for leak detection
Explore the Leak Testing Section
Leak Testing is used to ensure quality, tested and proven parts are supplied into the market. The use of leak testing equipment eliminates failures in the field.
Explore this section to find out more about the how TQC can help you with your leak testing requirements
- Overview
- Air Decay
- Helium
- Other Test Methods
- Leak Testing Services
- Standard Equipment
- Case Studies
- Automotive Brake Leak and Flow Testing
- Automotive Bedplate Leak Test Machine
- Battery Tray Leak Test Machine
- Chilled Beam Leak Test
- Flexible Leak Test Facility
- Fuel Tank Leak Testing
- Helium Leak Test Bench
- Helium Leak Testing of Automotive Fuel Pipes
- High Pressure Audit Leak Testing System with Datalogging
- High Speed Leak Testing of Pipe Fittings using Air and Helium
- High Speed Leak Testing of Plastic Vial for the Medical Industry
- Leak Test Facility for Water Valves
- Leak Test Cell with Robotic Handling
- Casting Leak Testing of Engine Blocks
- Medical Filter Leak Test Machine
- Medical Showerhead Leak Test Machine
- Plastic Fuel Rail Leak and Burst Test Machine
- Plastic Sump Pipe Leak Test and Assembly
- Small Medical Device Leak Test Machine
- Twin Station Leak Test Machine for Oils Sumps
- V6 Cylinder Head Leak Test Machine
- V6 Engine Leak Test Machine
- V8 Cylinder Head Leak Test Machine
- V8 Engine Block Leak Test Machine
- Valve Block Leak Test Machine
- Vauxhall Leak Test Machine
- Weapon Leak Test Machine
Water submersal leak detection/location using a dunk tank for complex assemblies and parts
Water submersal or dunk tanks are a widely used method for location of leaks in complex assemblies and products with air bubbles present around the leaking area.
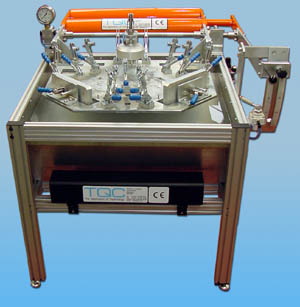
Most often, differential pressure or vacuum decay is used first to qualify a “tight” part before hand, one may then need to locate the leak afterwards using this underwater method. If the part leaks, simple decay of pressure does not show the leakage path. If a part fails the quantifiable test then one method of detecting the leak path is to submerge in water and look for bubbles.
All of these examples shown use the technique of submerging the part in water. Some of these examples were used as the only leak test method. All of these examples had complex sealing requirements prior to the pressure being applied.
When submerging a part the force required to push the part underwater against bouyency may be significant. To work out the force first, calculate the volume of the water displaced by the part, multiply by 10N (1KgF) per litre and then subtract the mass of the part. This calculation will indicate the submersal force require to hold the product underwater.
Each of the systems locate the part or assembly into a fixture. The assembly is then clamped into place either by hand operated toggle clamps or automatically. Some sealing areas and the length of seal are considerable, requiring significant seal forces to both compress the seal and overcome the forces generated by the internal pressure.
In all instances an operator makes a subjective visual check as to whether the part is good or bad. Clearly a bubble has to be formed, released and identified by observation so this technique is limited in its suitability.
For a printer friendly copy of the information on this page
Ultrasonic Bubble Testing
There is a technique applied by TQC where by bubbles leaving a part can be sensed and mapped using ultrasonics. The technique is similar to SONAR but on a smaller scale.
To find out more about how we can help you with your leak testing requirements:
We build all machines in-house, applying our 25+ years experience in specialised test and automated handling machines experience to the engineering projects we undertake. We offer customer support, backup and service call-out for all projects, whatever the size.
Get in touch with us to discuss your requirements and we will be happy to offer our professional advice and visit you at your site.
- Contact us online
- Email us or call us on 0115 950 3561