Leak Testing Case Studies: Battery Tray Leak Test Machine
Explore the Leak Testing Section
Leak Testing is used to ensure quality, tested and proven parts are supplied into the market. The use of leak testing equipment eliminates failures in the field.
Explore this section to find out more about the how TQC can help you with your leak testing requirements
- Overview
- Air Decay
- Helium
- Other Test Methods
- Leak Testing Services
- Standard Equipment
- Case Studies
- Automotive Brake Leak and Flow Testing
- Automotive Bedplate Leak Test Machine
- Battery Tray Leak Test Machine
- Chilled Beam Leak Test
- Flexible Leak Test Facility
- Fuel Tank Leak Testing
- Helium Leak Test Bench
- Helium Leak Testing of Automotive Fuel Pipes
- High Pressure Audit Leak Testing System with Datalogging
- High Speed Leak Testing of Pipe Fittings using Air and Helium
- High Speed Leak Testing of Plastic Vial for the Medical Industry
- Leak Test Facility for Water Valves
- Leak Test Cell with Robotic Handling
- Casting Leak Testing of Engine Blocks
- Medical Filter Leak Test Machine
- Medical Showerhead Leak Test Machine
- Plastic Fuel Rail Leak and Burst Test Machine
- Plastic Sump Pipe Leak Test and Assembly
- Small Medical Device Leak Test Machine
- Twin Station Leak Test Machine for Oils Sumps
- V6 Cylinder Head Leak Test Machine
- V6 Engine Leak Test Machine
- V8 Cylinder Head Leak Test Machine
- V8 Engine Block Leak Test Machine
- Valve Block Leak Test Machine
- Vauxhall Leak Test Machine
- Weapon Leak Test Machine
Client: Leading Automotive Vehicle Manufacturer
Part: Battery Tray
Machine supplied: Leak Test system with infeed and outfeed conveyors
Overview: This system was designed and manufactured in order to give the customer the ability to leak and flow test brake assemblies within their production environment. TQC developed this system alongside the client to allow them to supply quality, tested parts to their customers.
Download details of this system as a PDF
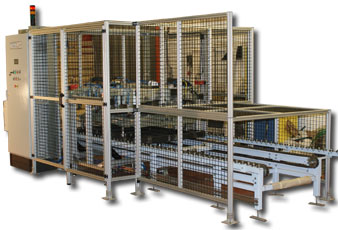
TQC have designed and manufactured a fully automatic solution to provide the final leak test to ensure an automotive battery tray is fit for purpose.
The tray is manufactured from pressed steel components welded together and then hand finished with a sealant to provide the leak tight chamber.
The leak test facility forms a chamber over the battery tray and clamps a seal down onto the flange area around the up turned lip of the battery tray. The seal is generated using a ‘P’ shaped neoprene seal.
The battery tray is transported around the conveyor system by a palletised system, each battery tray has it’s own TQC designed and manufactured dedicated pallet.
The test pressure is 16mbar and once the test pressure has been achieved it stabilises and is held for 60 seconds. During the 60 second time period the test pressure must not fall below 14 mbar otherwise the part fails the leak test.
The system is controlled via a PLC with all leak test parameters editable through the HMI.
The system maximum cycle time of 3.75 minutes (225 Seconds), in practice the system throughput is nearer to 90 seconds.
To find out more about how we can help you with your leak testing requirements:
We build all machines in-house, applying our 25+ years experience in specialised test and automated handling machines experience to the engineering projects we undertake. We offer customer support, backup and service call-out for all projects, whatever the size.
Get in touch with us to discuss your requirements and we will be happy to offer our professional advice and visit you at your site.
- Contact us online
- Email us or call us on 0115 950 3561